At the end of 2022, my colleague Artemio Villegas and I bought an Injection Machine together with the intention of going into business together. Our injection molder was from buster beagle 3d and came as a parts kit. Our project is still ongoing, and we have so far gotten decent results from our machine.
My role in this partnership was to use my experience with polypropylene to aid in troubleshooting any problems with our process. Additionally, I researched many aspects of plastic and injection molding. Neither of us started with any experience in injection molding, but now we are very close to launching an injection-molded product together. This project is an ongoing work in progress.
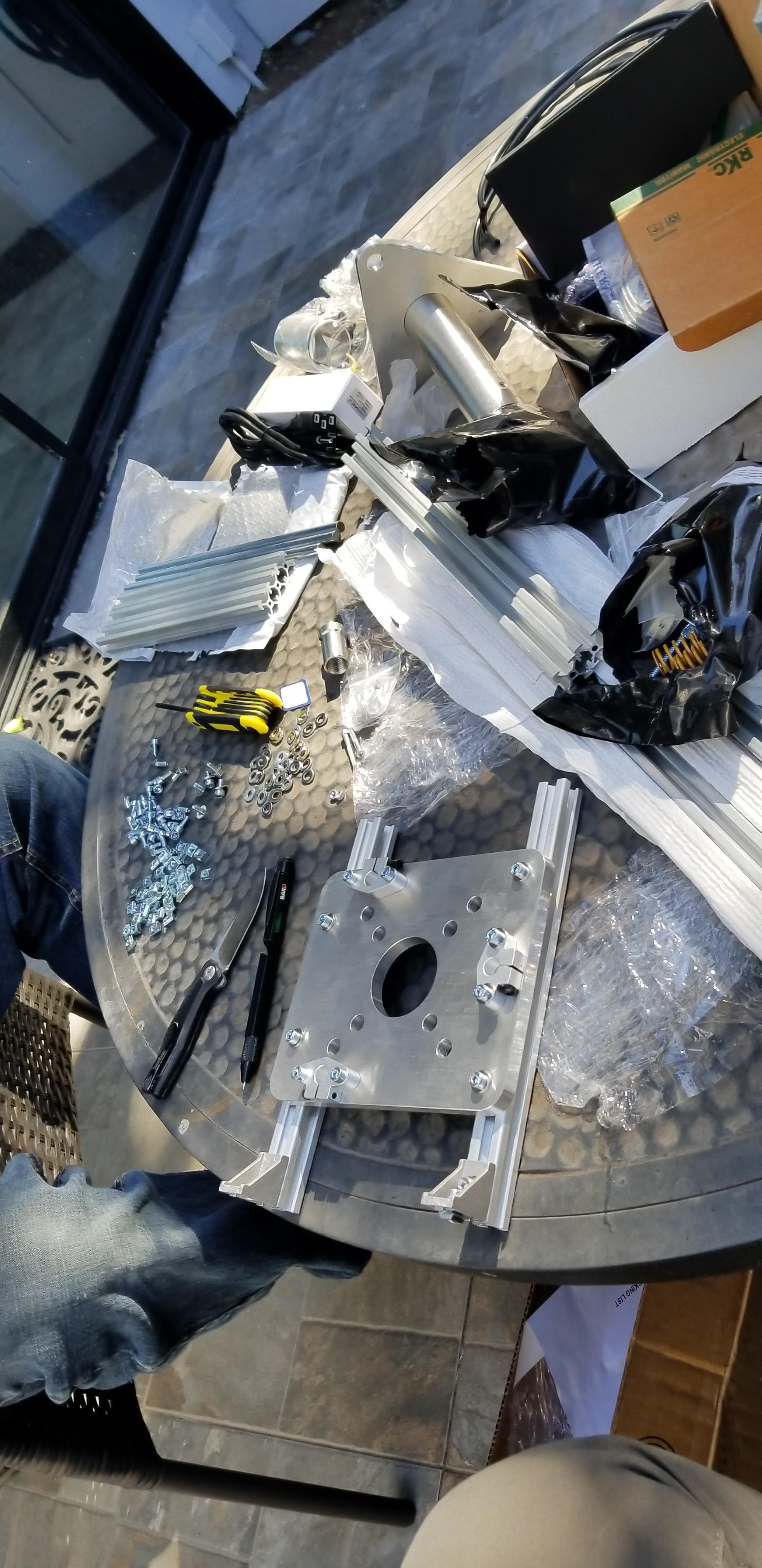
The Machine came as a parts kit that we had to assemble from stratch
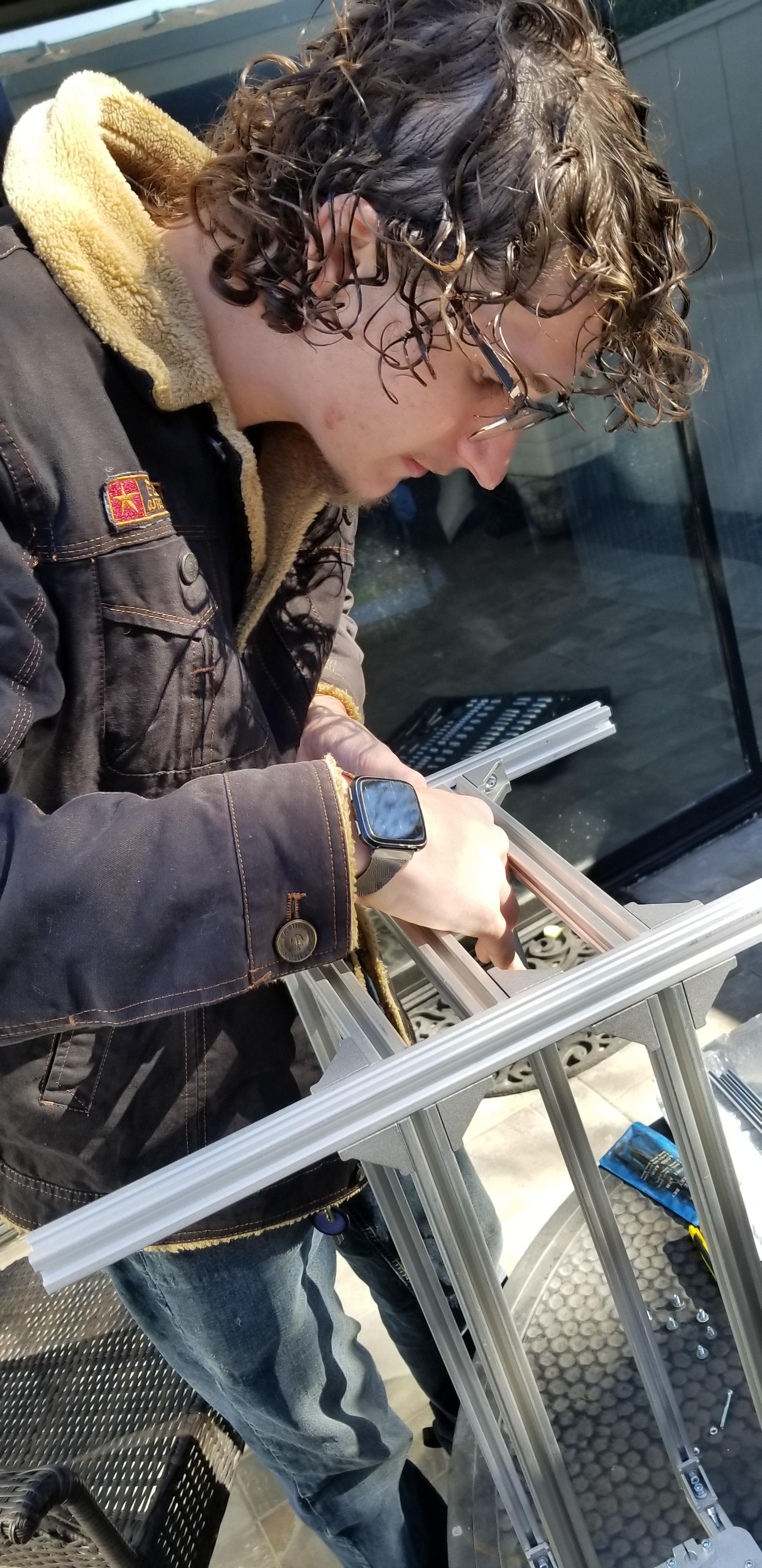
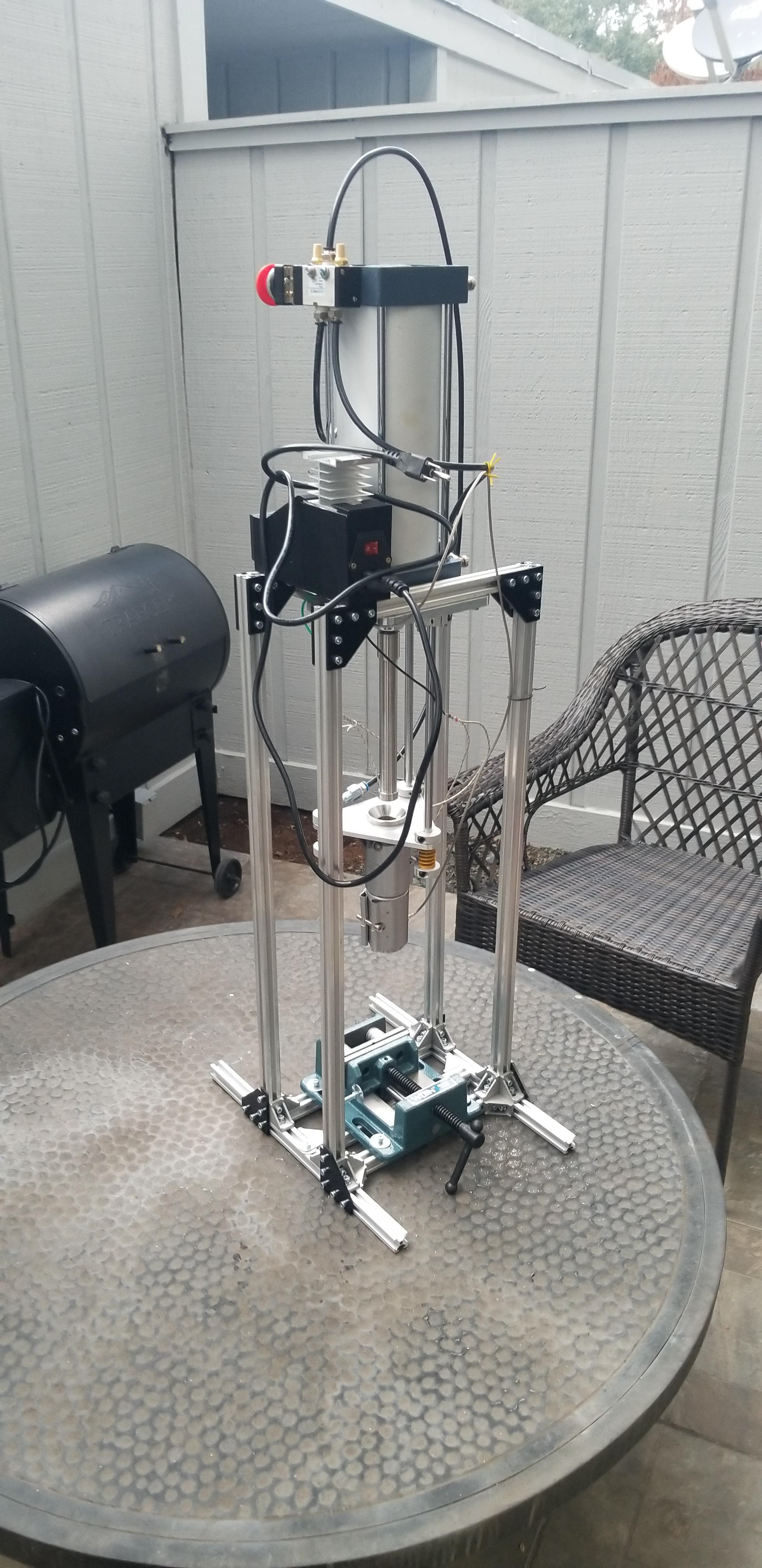
Here is what the machine looks like assembled
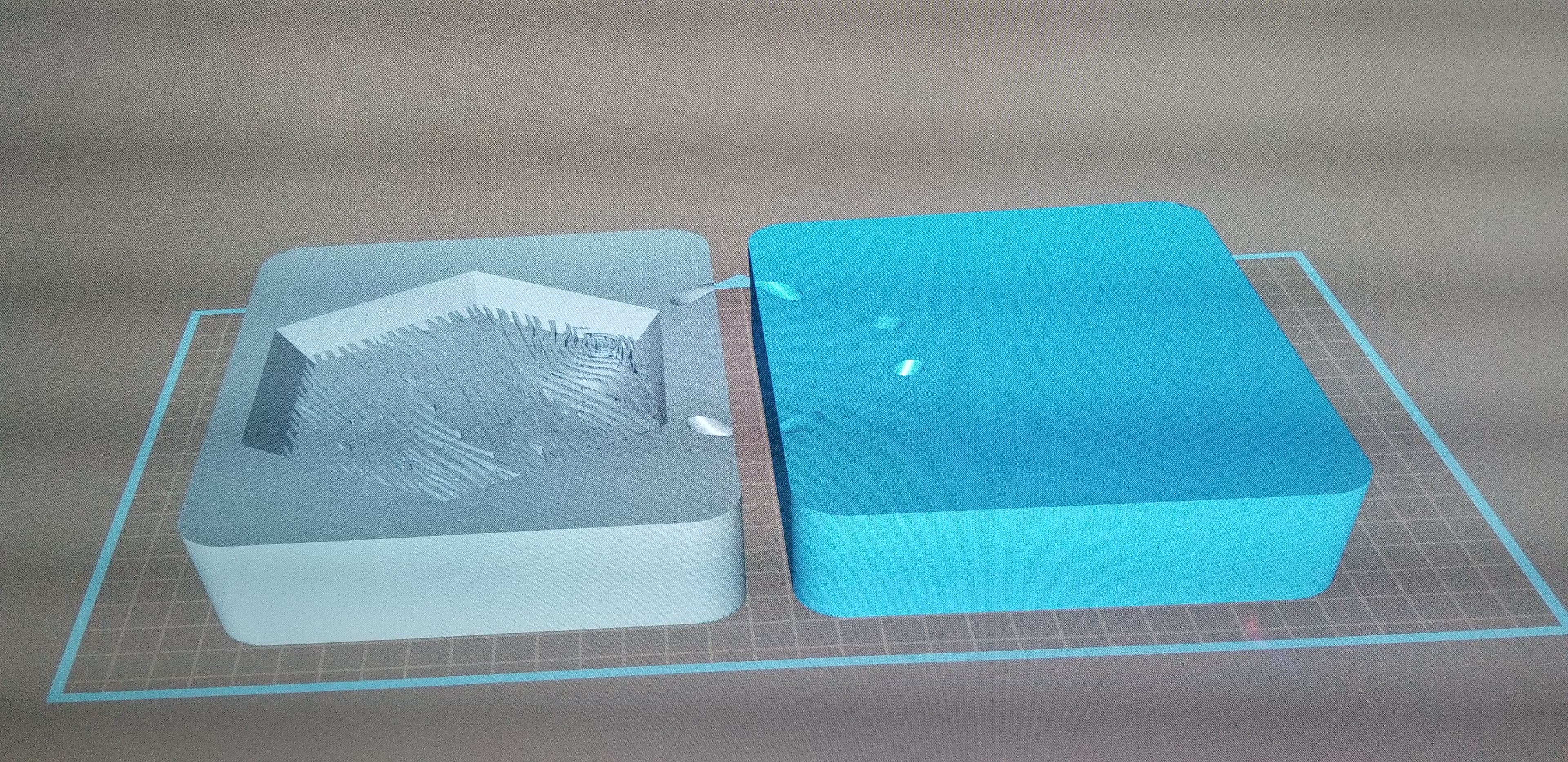
We designed the two halves of the mold with ports for the plastic to be injected into.
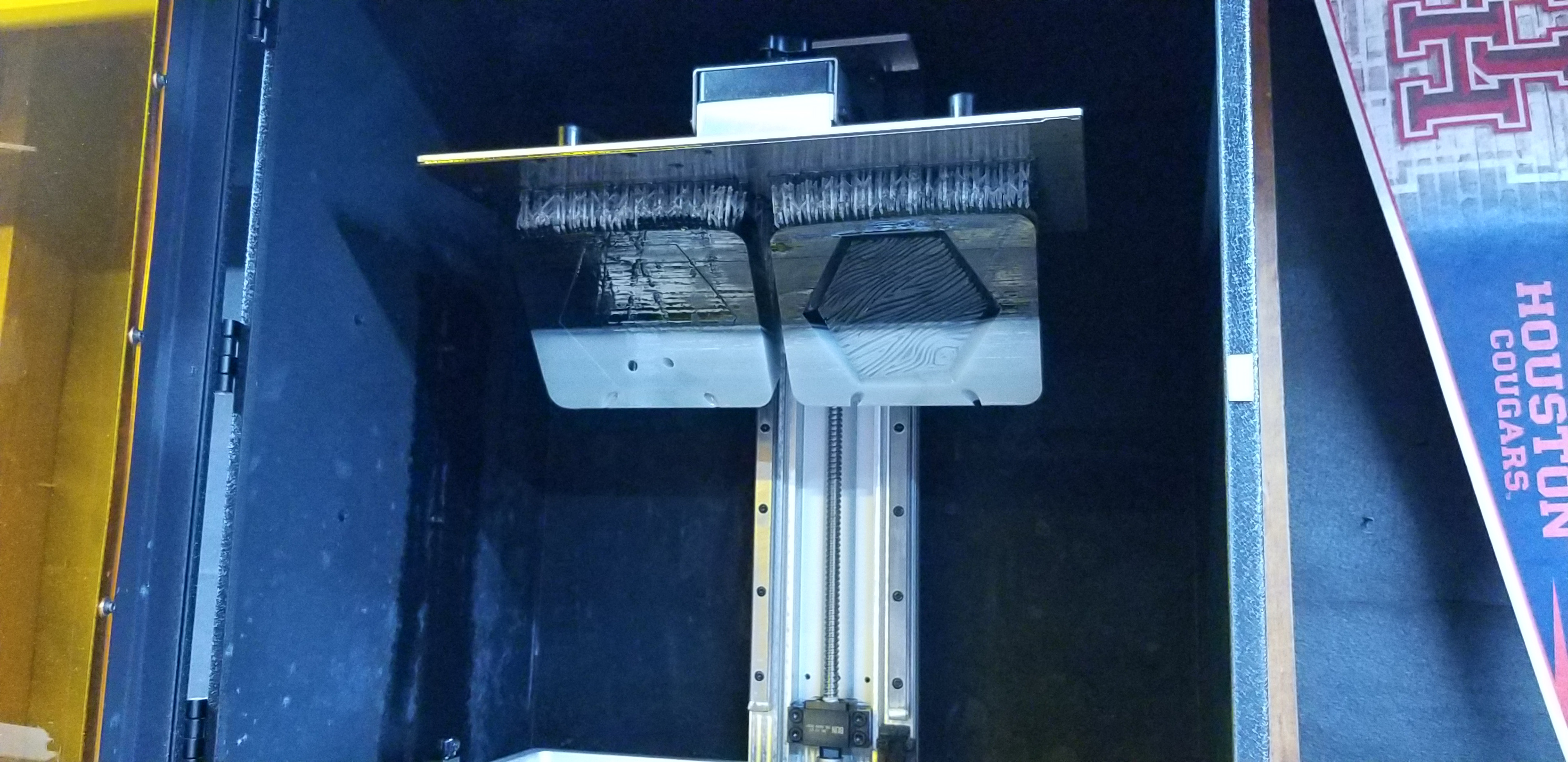
Our mold was resin printed out of a tought resin thatcan withstand the pressure.
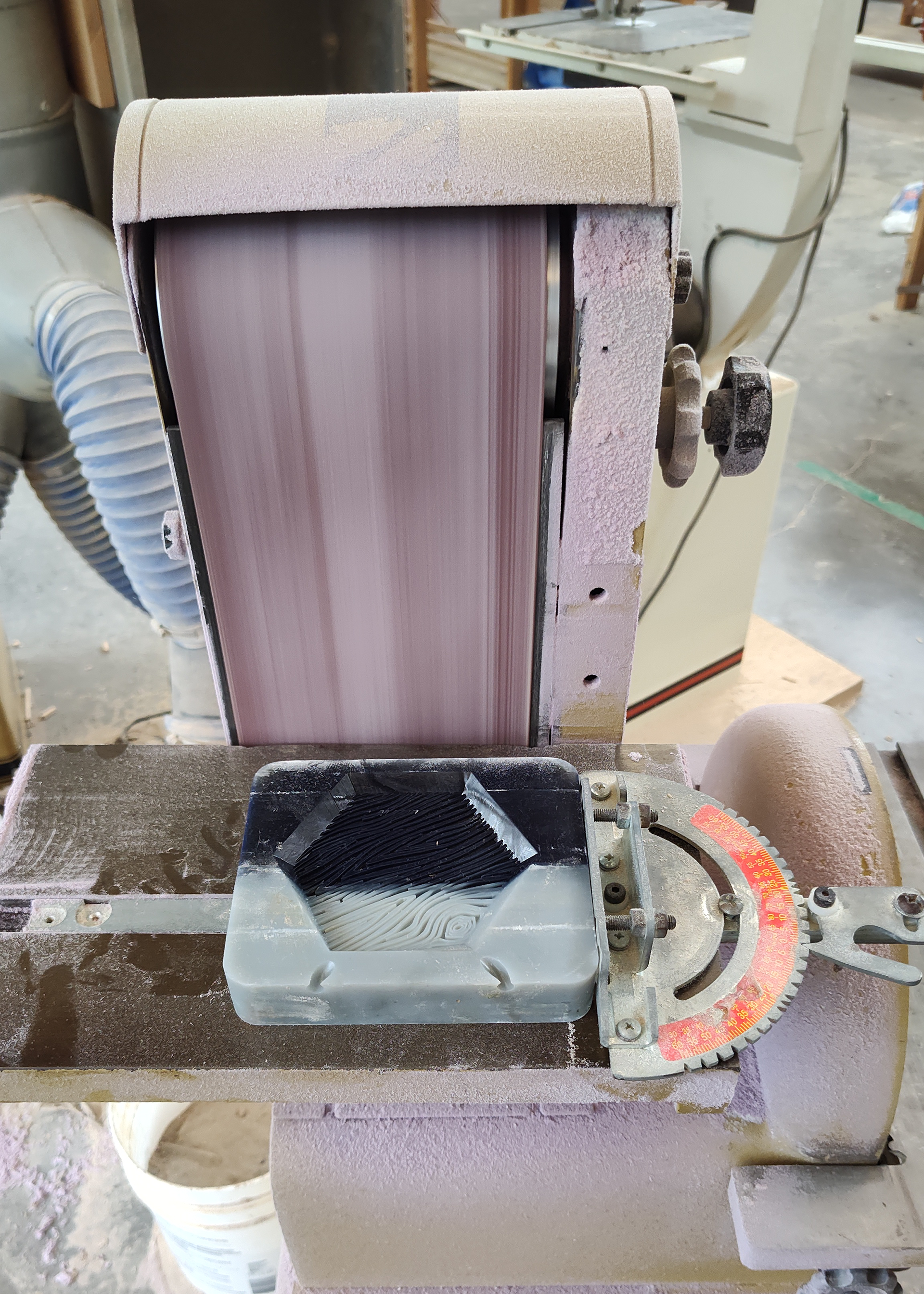
Our resin printed mold inserts needed to be fitted inside our mold carrier. Durring the resin printing they warped, luckily the product itself was uneffected.
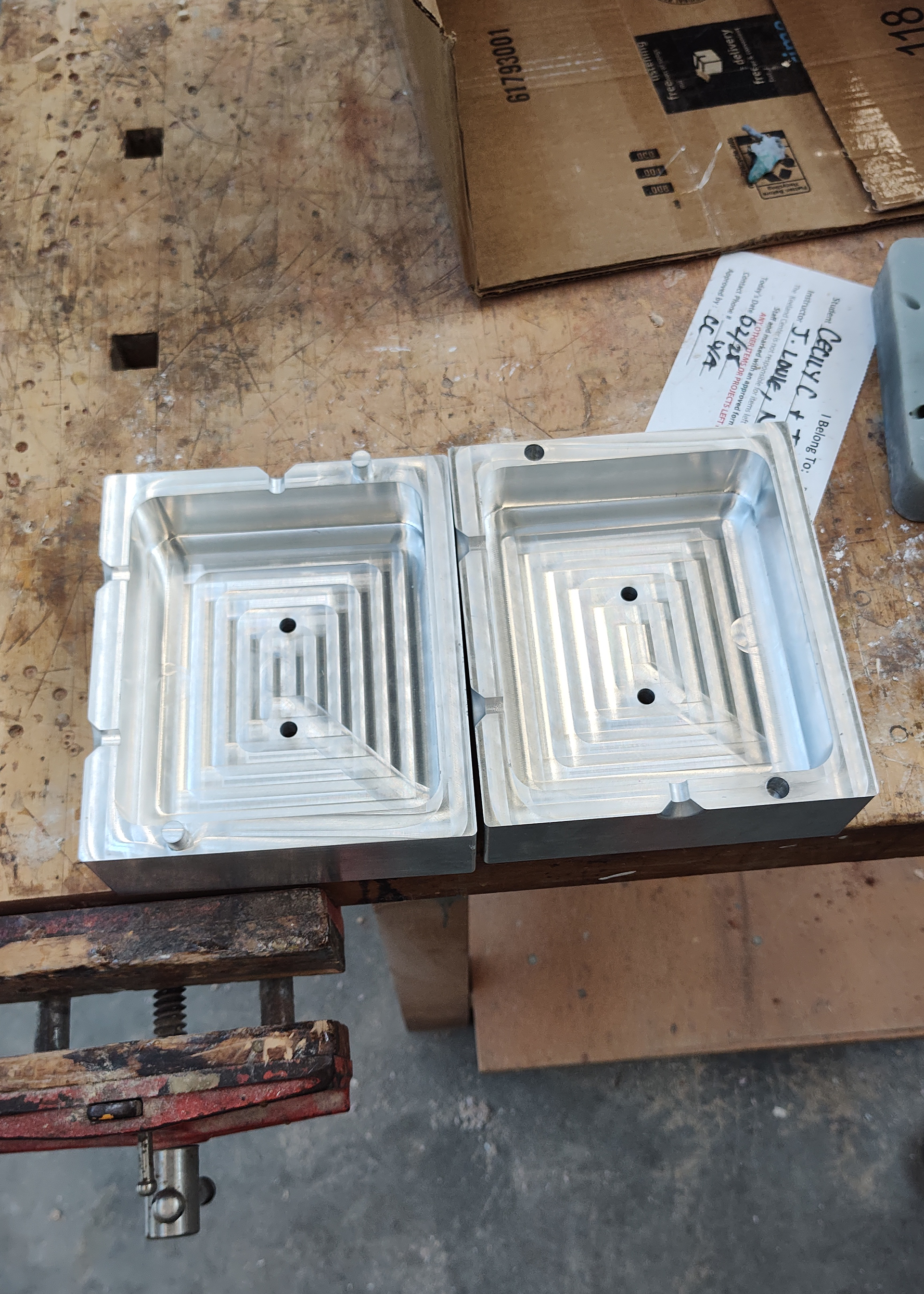
We had a mold carrier machined for us.
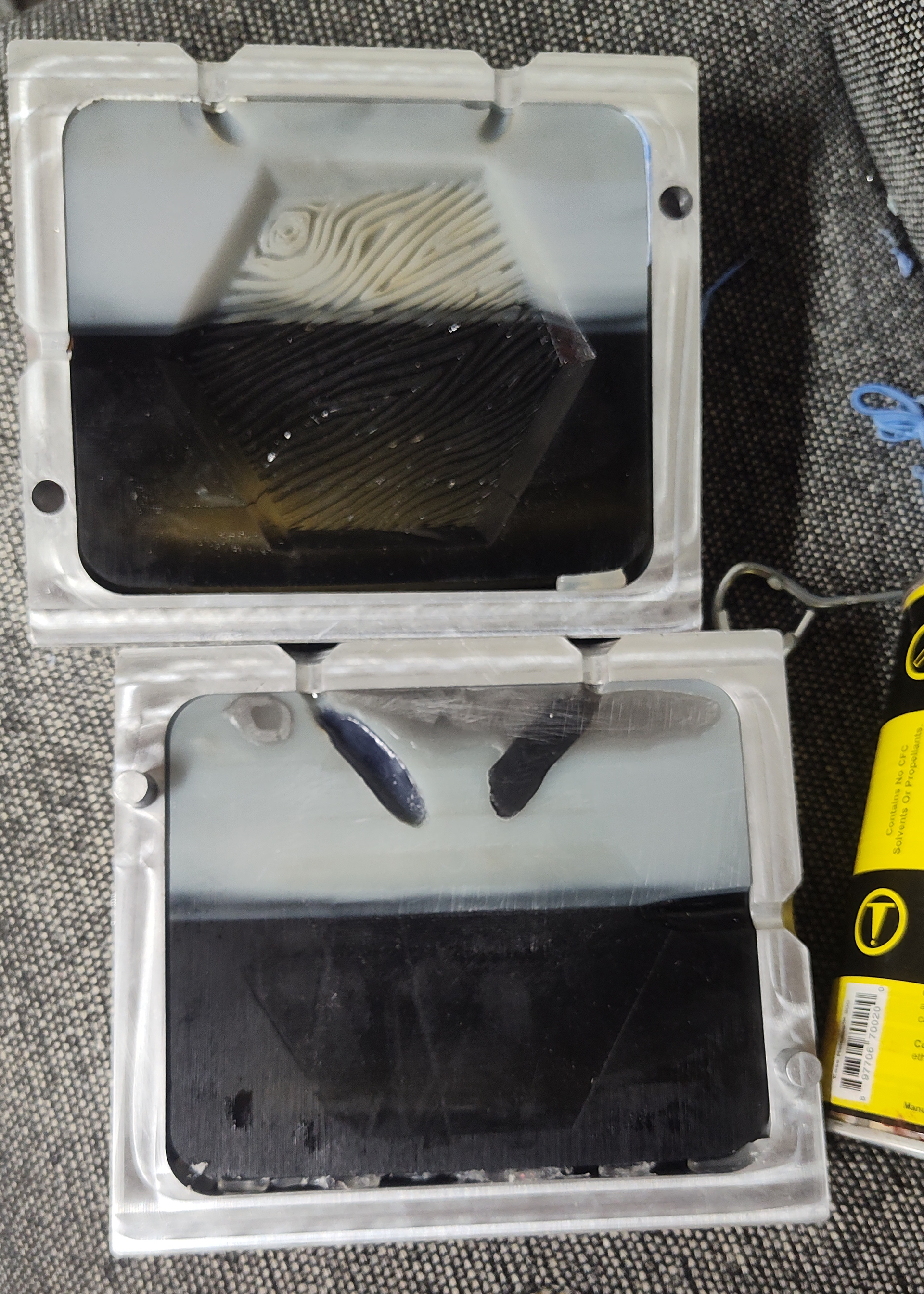
With the mold finished, we were ready to get started.
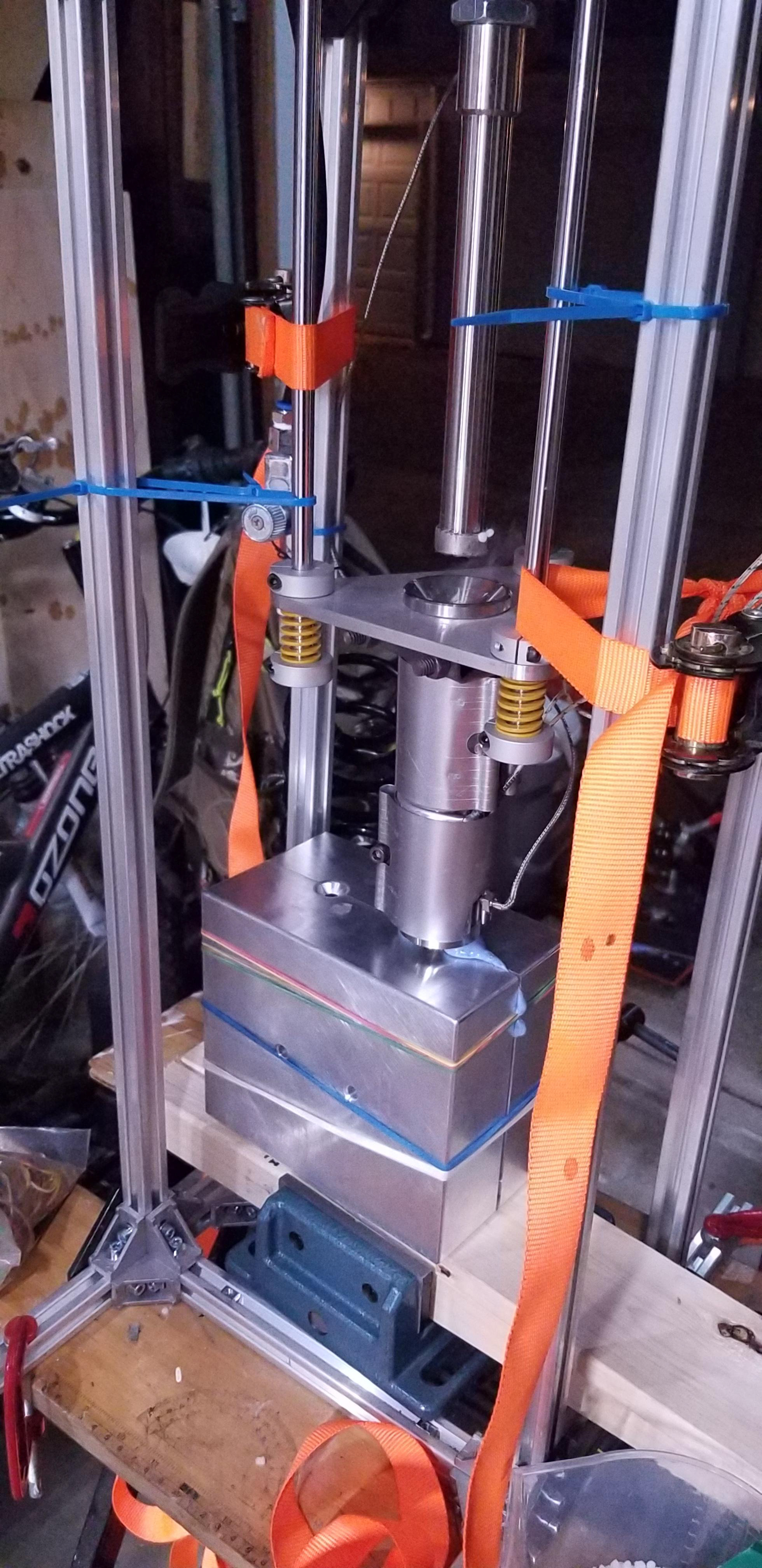
Here you can see the injection molder in action. This attempt we had inadequite clamping nd you can see the flashing squeeze out as a result.
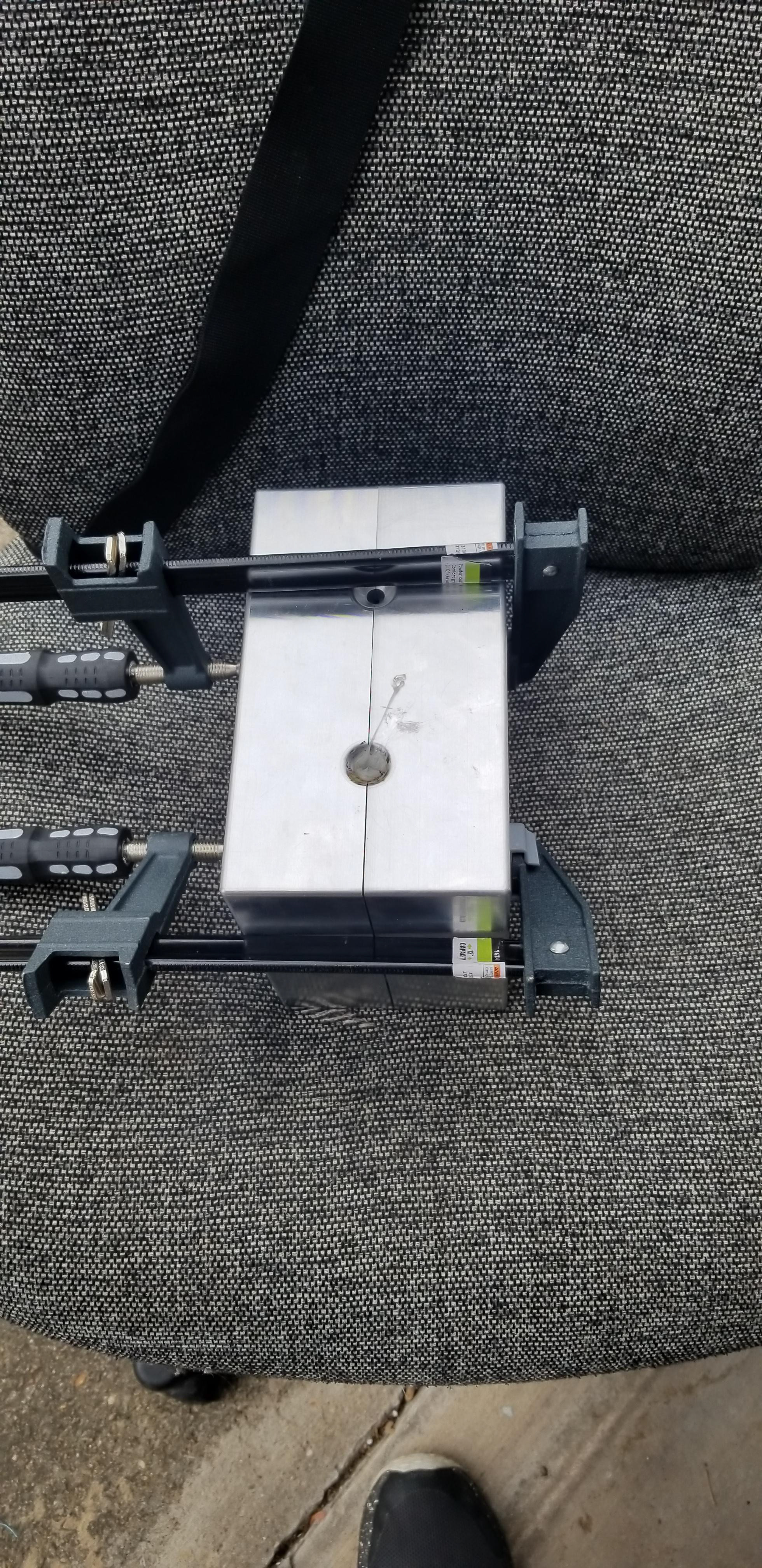
We used clamps to reduce the flashing but that didn't prevent short shots.
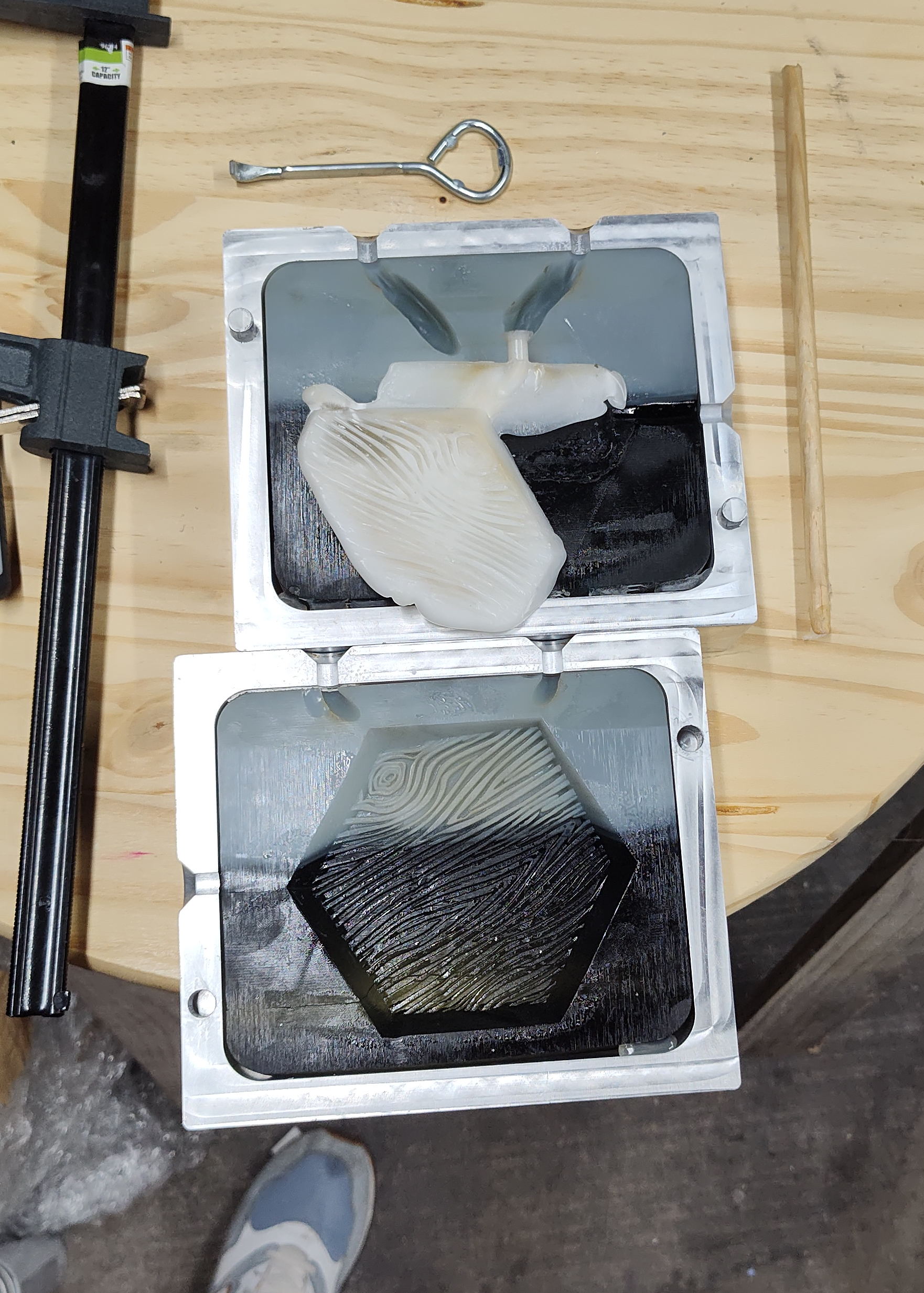
I spent a lot of time tweaking the plastic mix and the tempitures to get better results. Short shots are caused in part by the plastic cooling early and solidifying.
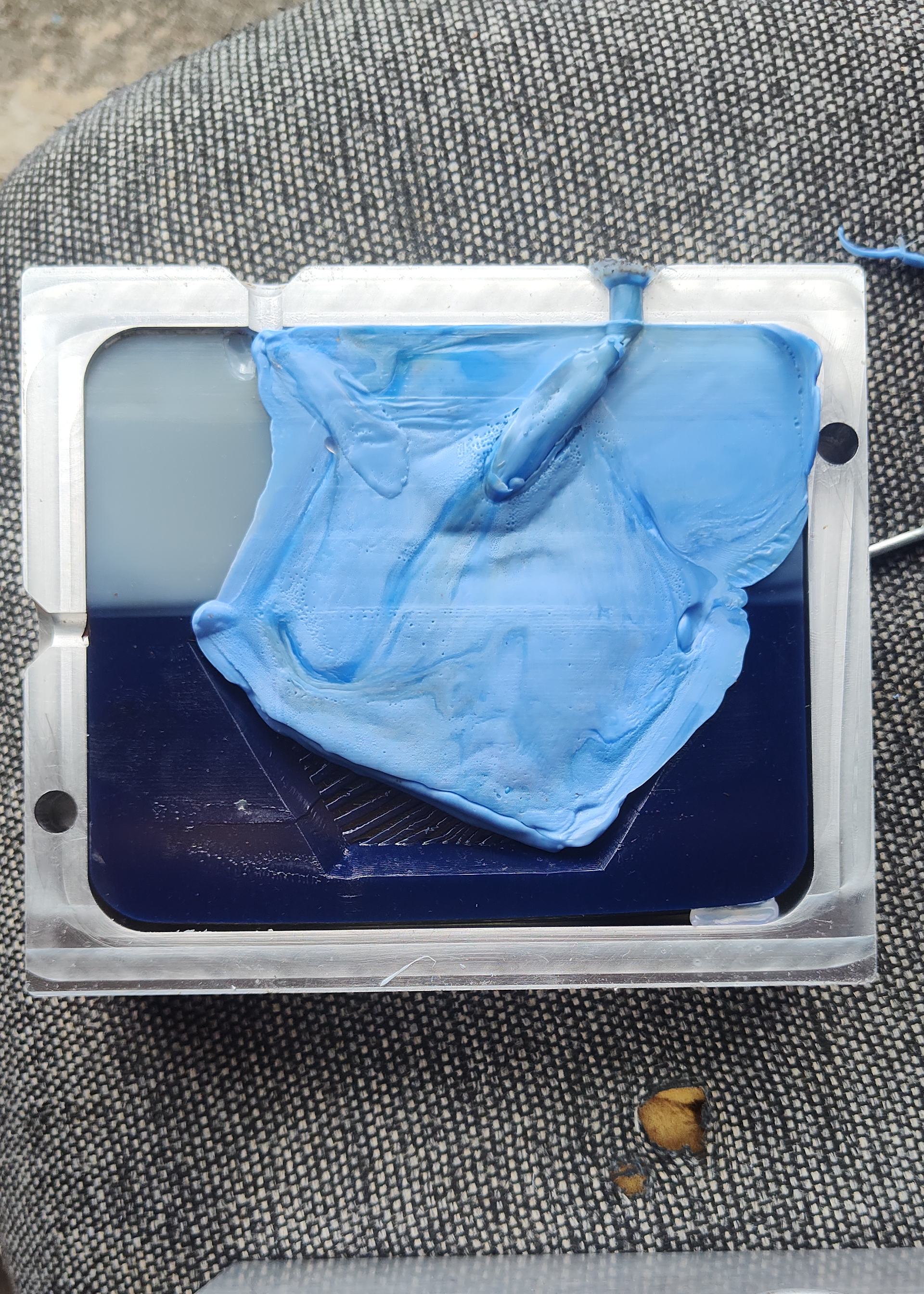
We kept getting closer by preheating our mold but the recycled material simply wasn't consistent enough with our setup.
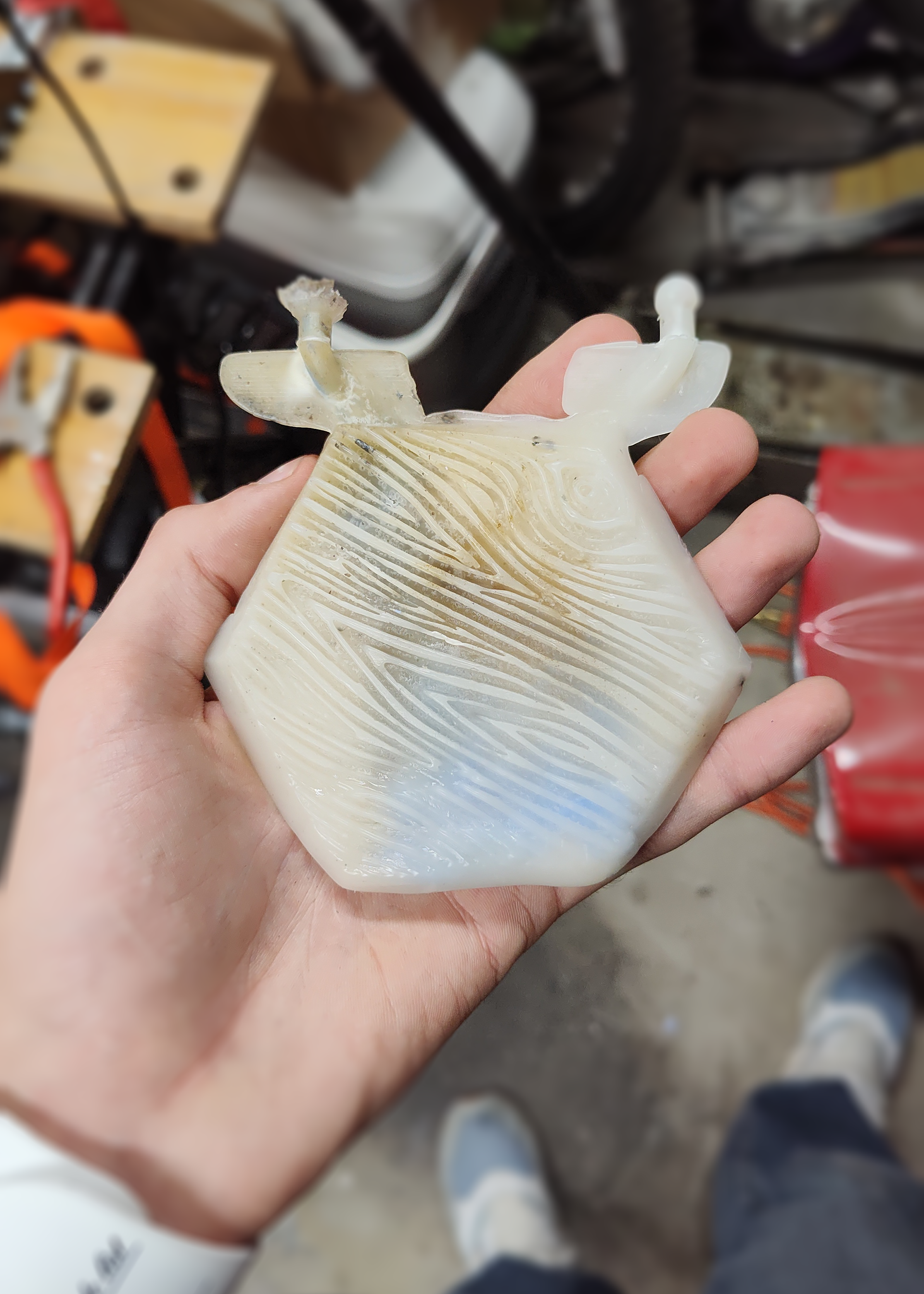